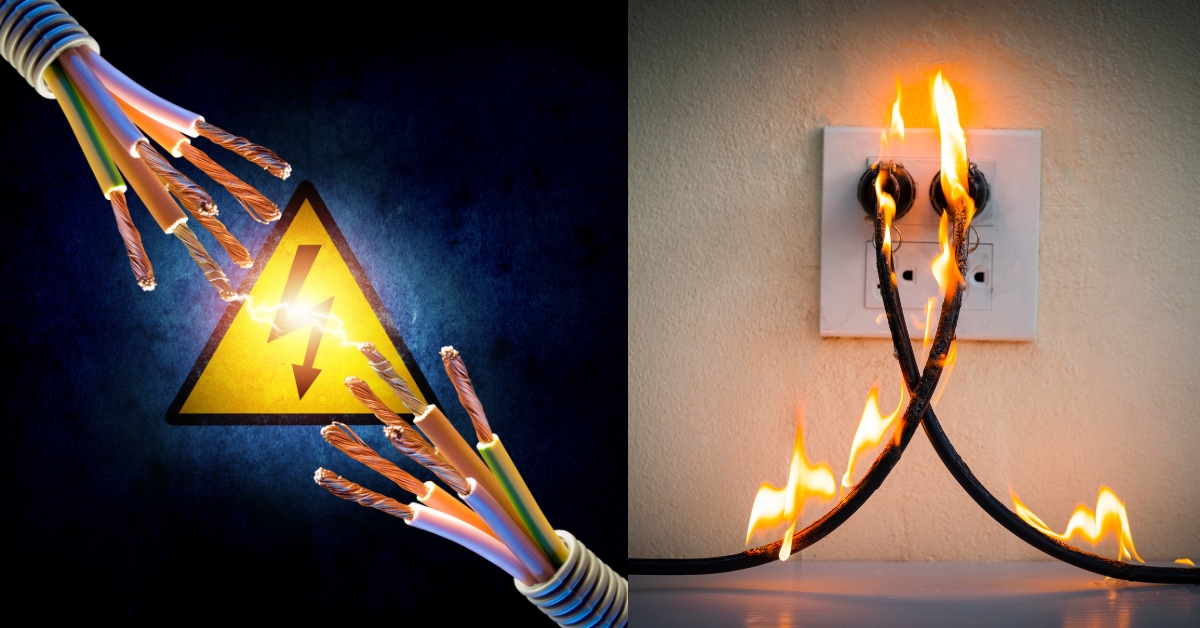
Understanding the Importance of Electrical Connectors
Connectors serve as the interface between different components in a power system, ensuring that electricity flows reliably from one point to another. They must handle not only the rated current and voltage but also environmental conditions like temperature fluctuations, moisture, and vibration. Their role in system safety is crucial: a poor-quality or improperly installed connector can become a weak link, jeopardizing the entire system’s reliability.
Choosing the Right Connector for the Application
Selecting the right connector begins with understanding the application’s electrical and environmental requirements. For low current applications, high-performance connectors with precise contact resistance and insulation standards are necessary. In high-power scenarios, heat dissipation and locking mechanisms become equally important. Compatibility with cable types, conductor materials, and system voltages must be considered. Following guidelines from established standards, such as IEC or UL, also helps ensure that connectors perform safely over time.
Connector Material and Design Considerations
The materials used in connectors affect conductivity, corrosion resistance, and mechanical strength. Copper and its alloys are commonly preferred for their high conductivity. Contact surfaces are often plated with tin, silver, or gold to enhance performance and durability. The connector design must ensure secure mating with minimal contact resistance. Mechanical features such as locking mechanisms, strain reliefs, and protective housings add layers of safety to the power system by preventing accidental disconnection and environmental ingress.
Installation Best Practices for Long-Term Safety
Proper installation techniques are critical to connector performance. This includes correctly stripping the insulation, using the right crimping tools, and ensuring firm mating between contacts. Over-tightening or under-tightening terminal screws can result in poor connections or damage. In industrial settings, torque specifications must be strictly followed. Additionally, connectors must be appropriately labeled to facilitate safe maintenance and troubleshooting in the future.
Environmental Protection and Insulation
Environmental factors such as moisture, dust, and corrosive substances can degrade connector performance over time. Using connectors with adequate IP (Ingress Protection) ratings helps protect against these conditions. Weatherproofing accessories such as boots, sealants, or enclosures can further enhance protection. In indoor environments like control panels or Low Current System In India, connectors with flame-retardant insulation materials add an additional layer of fire safety.
Testing and Quality Assurance
After installation, connectors should undergo thorough testing to verify mechanical and electrical integrity. Continuity tests, insulation resistance checks, and thermal imaging can reveal potential faults. Periodic inspections during the system’s life cycle help identify signs of wear or degradation. Incorporating connectors from certified and quality-assured suppliers ensures that every connection point meets the performance and safety expectations of the system.
Connector Maintenance and Inspection
Like all components, connectors require routine maintenance to ensure continued performance. Visual inspections can detect discoloration, corrosion, or physical damage. Loose connections should be retightened as per specifications. In environments with high vibration or thermal cycles, connectors should be checked more frequently. Documentation of maintenance activities helps in creating a reliable and safe operational history of the power system.
The Role of Skilled Professionals and System Design
A safe power system is the result of skilled design and installation. Professionals trained in connector technologies can make informed decisions on product selection, installation techniques, and safety measures. Companies like Top Electrical Solution Company in Rajasthan provide expert solutions for both high and low-voltage systems, helping industries build safe, reliable, and scalable electrical infrastructures.
Conclusion
Connectors may seem like minor components in a power system, but their role in ensuring safety and performance is massive. From selection and installation to maintenance and inspection, every step must follow best practices to prevent failures and safeguard assets. With growing dependence on stable and uninterrupted electrical systems, industries must prioritize connection confidence as a core pillar of electrical safety. Manikaran Enterprises continues to lead by example, ensuring excellence in every aspect of power system assembly and implementation.